Fiber Laser Welding Equipment
Effortless welding that enhances overall efficiency and productivity.
Featuring precision laser technology, ergonomic design, and an intuitive operating system, DNE’s welders ensure clean, uniform welds with minimal post-processing.
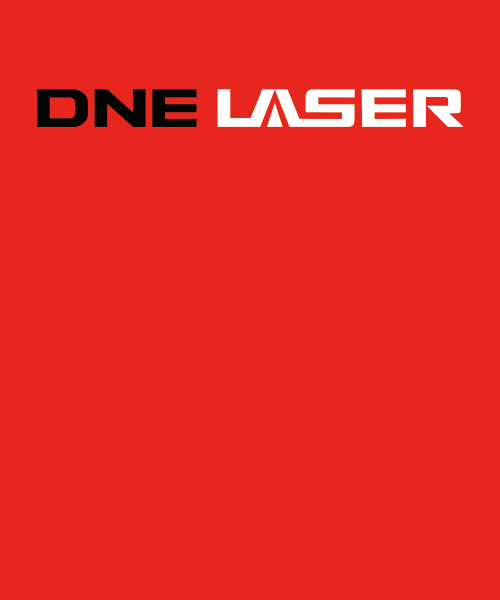
When compared to traditional welding methods, DNE’s handheld laser welders present a lightweight, compact, and adaptable solution. These units are user-friendly across various materials such as stainless steel, carbon steel, aluminum, galvanized steel, and copper. They boast up to four times faster welding speeds, increased weld strength, and decreased porosity. Offered in both standalone and fully automated welding stations, the DNE handheld fiber laser welder is the complement for any shop.
Contact us to discuss your requirements with our applications team. We’ll work with you to ensure you get the best solution for your application, working environment, and production goals.
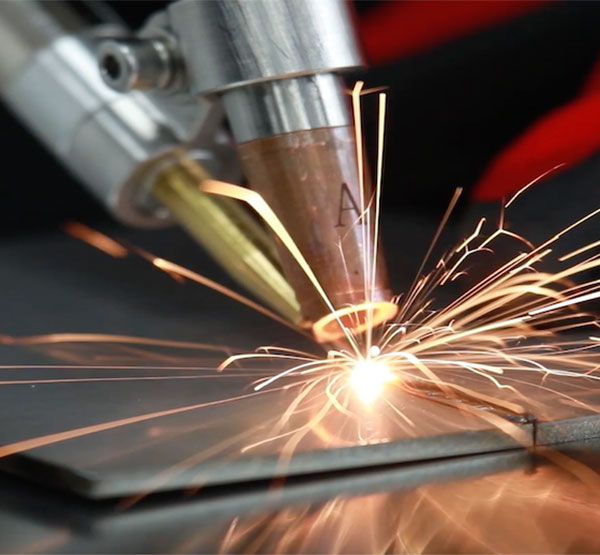
Discover Your Fiber Laser Welding Solution:
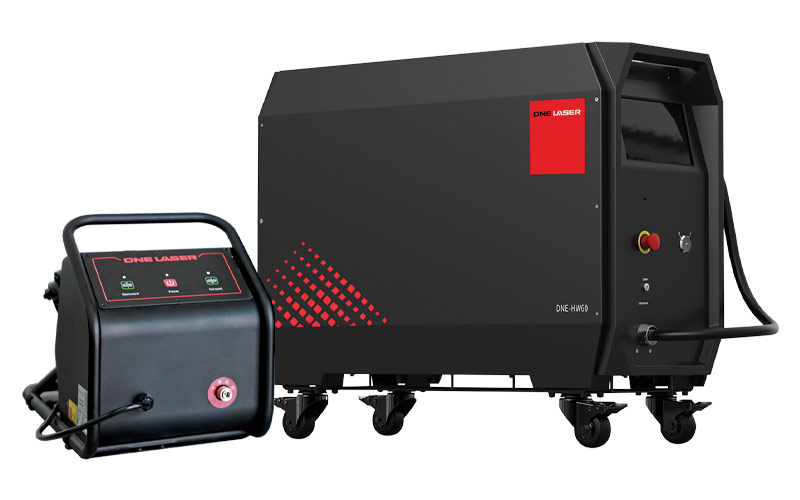
Frequently Asked Questions
Why would I want to use a laser welder over MIG or TIG welding?
Laser welding delivers high-quality welds with minimal heat input. The focused laser reduces distortion of the base metal due to heat and maintains material integrity, resulting in improved weld quality. The concentrated beam allows precise control of heat input based on the desired weld depth and width. This flexibility enables both full penetration welds and thin-sheet welding without significant material damage.
Laser welding is non-contact, reducing the risk of contamination. It offers fast welding speeds, making it efficient for production. While some limitations exist, laser welding can join a broader range of materials, including dissimilar or painted materials, with limited post-process cleanup. Last, laser welding can be done with limited training and experience allowing shops to adapt to an
everchanging workforce.
How thick of material can I weld?
In the case of laser welders, we focus on penetration depth and not necessarily material thickness. Each welder model name indicates the maximum weld penetration that the welder is designed to achieve. For example, the HW-60 has a 6mm (.24”) weld penetration, while HW-40 has a 4mm (.16”) weld penetration. All weld specifications should be considered when choosing a solution.
How portable is the welder?
The welders weigh approximately 55 lbs to 86 lbs and can simply be wheeled to the location needed. Very comparable to traditional MIG / TIG welding carts.
What is needed for the electrical? Do I need gas?
The welder requires 220V single-phase and draws 22 amps (HW-30), 25 amps (HW- 40) or 28 amps (HW-60). Gas is required, either Argon or Nitrogen at 99.99% purity.
Do I need to use wire? Is it the same as MIG/TIG wire?
The welder comes standard with wire feed but can be operated with or without wire. As with other methods, the wire will help fill larger gaps. However, the feed also works to assist the operator in controlling the speed of the gun during the weld pass by ‘pushing’ off the workpiece. Typically, a loose arm and letting the gun do the work yields the best results. Standard welding wire is used and should be selected based on material type or thickness.
Do I need a perfect fit up on parts?
Fit-up can be important to laser welding as the technique to laying a bead is different and “walking the cup” is not utilized. DNE welder’s ability to offer a “wobble” function, which moves the beam back and forth up to 4 mm, helps to support the filling of gaps in part fit-up.
Are laser welders safe?
As with any manufacturing tool the proper safety precautions need to be taken with a laser welder to ensure operator safety. Since a laser is used in the welding process protection of the eyes is critical. DNE’s systems incorporate two critical safety features. First, which is included with the laser welder, is an integrated laser safety helmet that is directly connected to the welder. Should the helmet be removed during operation, the laser automatically shuts off. Additionally, the welder includes a part contact interlock, cutting operation if contact with the base material is lost. Ultimately shop safety is the responsibility of the user and can be addressed through passive protection such as laser safety enclosures/barriers. DNE offers a variety of protection systems including fully enclosed fixed enclosures, portable enclosures without roofs, and paneled barriers. When assessing the potential EH&S impacts of a laser welder the following standards should be reviewed and understood.
ANSI Z136.1 – Safe Use of Lasers
As the parent document of the Z136 series of laser safety standards, the Z136.1 is the foundation of laser safety programs for industry, military, research and development (labs), and higher education (universities).
ANSI Z136.9 – Safe Use of Lasers in Manufacturing Environments
Intended to protect individuals with the potential for laser exposure when lasers are used in manufacturing environments, this standard includes policies and procedures to ensure laser safety in both public and private industries as well as product development along with testing.
ANSI Z136.7 – Testing and Labeling of Laser Protective Equipment
Provides reasonable and adequate guidance on the test methods and protocols used to provide eye protection from lasers and laser systems.
Additionally, there are many laser safety training options available, such as through the Laser Institute, which provides more insight into hazard analysis or the administration of a laser safety program for an organization. (Link for reference: https://www.lia.org/)
Request Information
If you're looking for a partner who will take the time to discuss your application, set you up with the best technology for the job, and support you from installation to training and ongoing tech support, you've come to the right place. Contact us for a prompt quote, application review, or system demo.
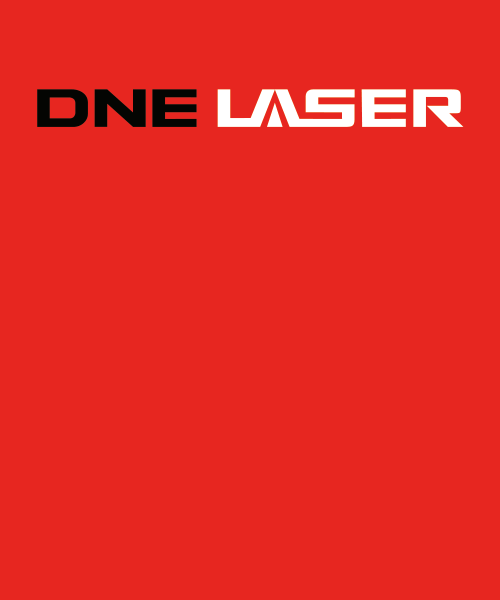
DNE LASER, wholly owned by the Bystronic Group, was established to provide innovative fab processing technologies to provide end users with competitive advantages and realize greater success. Backed by Bystronic, and a production base of more than 80,000 square meters, DNE focuses on the R&D, production, and sales of fabrication equipment. Since 2008 DNE has provided solutions for the automobile, mechanical equipment, electrical equipment, sheet metal, precision parts, hardware products, aerospace, and shipbuilding industries.
Today, with nearly 10,000 users worldwide, its products are sold in more than 100 countries — providing comprehensive solutions to sheet metal processing and automation.
DMS is the exclusive provider of DNE systems in New England.