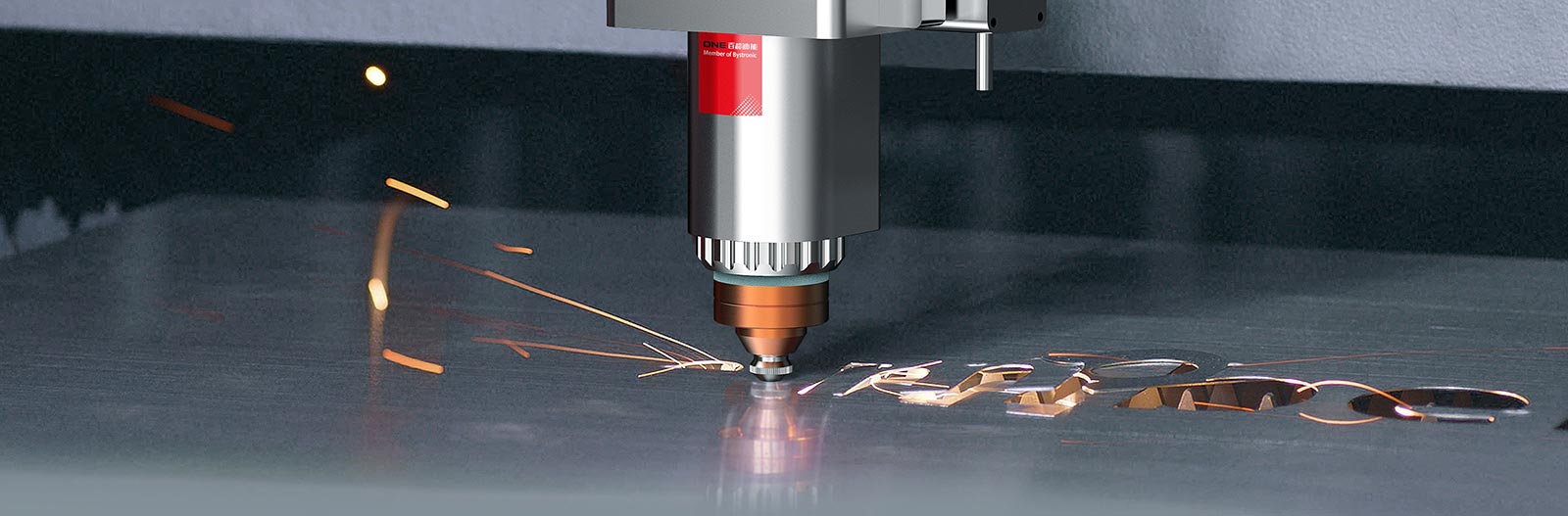
From their high precision and speed to reduced cost per part, lasers should be the first consideration for any new equipment investment. Here are some of the ways laser-cutting technologies are surpassing plasma.
Cost Per Part
Reduced Expense: Although the initial investment may be more than plasma, laser cutting machines deliver a reduced cost per part by eliminating or reducing downstream post-processing, removing the need for expensive gas contracts, and simplifying maintenance.
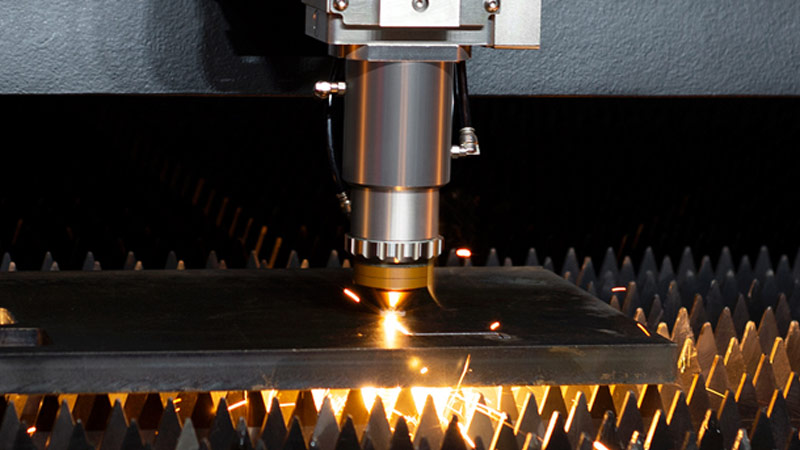
Precision & Detail
High Accuracy: Laser cutters can achieve very fine details and intricate designs, making them ideal for projects requiring precision. Laser cutting systems are capable of achieving ± 0.002″ accuracy.
Clean Cuts: Lasers produce cleaner edges with a minimal burr, reducing the need for additional secondary operations or finishing processes. Plasma cutting produces a wider kerf and can generate excess dross and slag.
Material Versatility
Wide Material Range: Laser cutters can handle a wide variety of materials and thicknesses. From thin sheet metal to mild steel over 7.0″ thick, lasers like the DNE D-Giant offer greater versatility and flexibility. Plasma cutters are only effective on conductive materials, limiting material applications and effective thickness range.
Heat-Affected Zone (HAZ)
Base Material Change: With their concentrated beam, lasers create a smaller heat-affected zone (HAZ). This localization of heat also reduces the effects on the base material’s overall structure and strength, such as localized hardening. Laser cutting generates the smallest HAZ among all the thermal cutting processes. A large HAZ can make predicting a material’s bending response challenging, as heat can affect characteristics such as spring back.
Sensitive Materials: Lasers are ideal for materials that are sensitive to heat, such as thin materials and certain plastics and composites. Lower heat leads to less overall warping and distortion of the material in thin materials, while precise laser control prevents delamination in composites or melting plastics.
Environmental Considerations
Less Smoke: All thermal cutting methods produce hazardous smoke and fumes. However, laser cutting tends to produce less smoke compared to methods like plasma cutting, which can be beneficial for air quality. Quality laser systems have integrated fume extraction, improving operating conditions.
Safety: Laser cutting typically generates less noise and fewer sparks, making it a safer working environment. Plasma cutters also produce certain forms of radiation, such as ultraviolet, which can be dangerous over time and cause permanent damage to the eyes and skin. Laser cutting systems have a safety enclosure that protects operators during use and are interlocked to ensure that protection is properly maintained.
In Summary…
DMS supports a full line of laser marking and cutting systems to meet a variety of applications. Contact us today to discuss how investing in a new laser system can be an advantage for your business.