Intro to Laser Marking
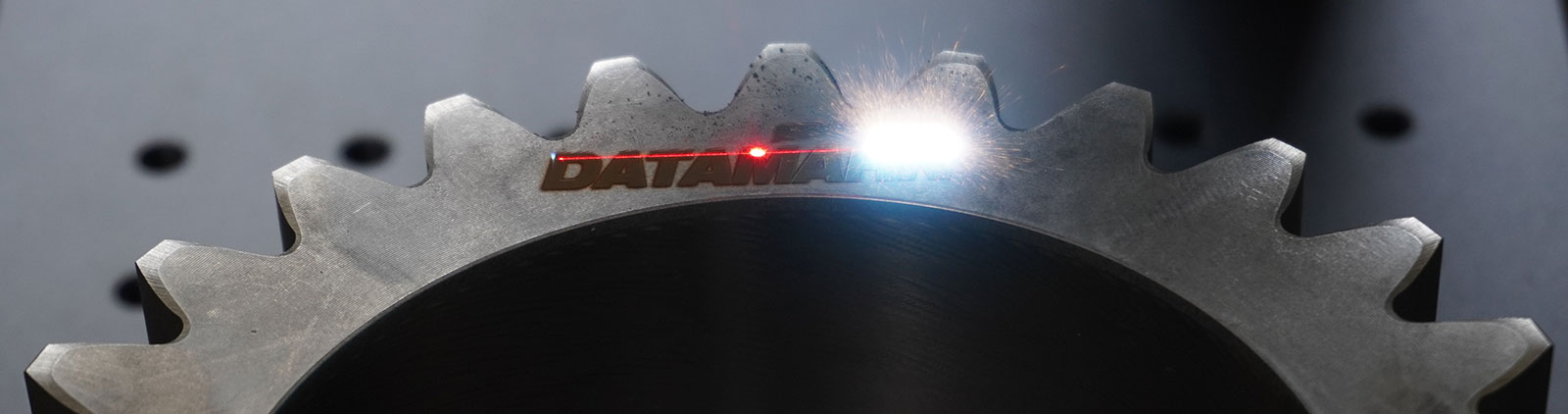
Fiber lasers, CO2 lasers, and diode lasers are all commonly used for marking applications, each with their unique attributes. Let’s compare these three types of lasers for part marking based on several key factors.
1. Wavelength
Fiber Laser: Operates in the infrared range, typically 1,064nm. This wavelength is ideal for marking metals and some plastics. Additional flexibility can be realized by utilizing a MOPA (Master Oscillator Power Amplified) laser, where both laser frequency and pulse can be adjusted in a wide range to maximize effectiveness of the laser in a specific material or application.
CO2 Laser: Operates in the far-infrared range (around 10,600nm). It is well-suited for marking non-metal materials like wood, glass, ceramics, and plastics. Provides minimal laser adjustments.
Diode Laser The wavelength depends on the type of diode used, but usually falls in the range of 808nm to 980nm. Typically, these are lower power lasers, less than 10 watts.
2. Marking Speed
Fiber Laser: Known for its high marking speed, making it suitable for industrial applications where productivity is crucial. The X/Y movement of the laser is controlled by a laser scan head (galvo head) where the mirrors only need to move a short distance to trace the mark. The high speed is also useful for deep marking applications, as the material removal rate can be faster than other types of lasers.
CO2 Laser: Generally slower than fiber lasers, as the laser head operates on a gantry system. Still provides adequate marking speed for many applications.
Diode Laser The marking speed is moderate, falling between fiber and CO2 lasers.
3. Marking Quality
Fiber Laser: Offers excellent marking quality, with high precision, fine details, and the ability to produce high-contrast marks on metals.
CO2 Laser: Provides good marking quality on non-metal materials, although it may not achieve the same level of precision as fiber lasers on metals.
Diode Laser The marking quality is usually sufficient for most craft applications in plastics and some metals, but it is not as precise as fiber or CO2 lasers.
4. Maintenance and Cost
Fiber Laser: Typically requires less maintenance and has a longer lifespan than CO2 lasers. Initial equipment cost is usually higher. On average, high-quality fiber lasers can last from 50,000 to 100,000 hours of operation before requiring significant repairs or replacement. With all mirrors contained within the marking head, maintenance requirements are minimal and manual adjustments are not required.
CO2 Laser: May require more maintenance, especially with the components. The most significant maintenance item is the laser tube, with a lifespan of only 2,000 to 10,000 hours, depending on use and quality of the tube. CO2 lasers also require active cooling via water systems, adding to the complexity and maintenance. Mirrors and lenses may require replacement and maintenance. Setup can be more involved than a fiber or diode laser. The initial equipment cost is often lower than fiber lasers. The performance of the laser can also be affected by the alignment of multiple mirrors in the system.
Diode Laser Generally, these lasers have a lower initial cost and require less maintenance than both fiber and CO2 lasers. Simple and low maintenance. Most often not serviceable.
5. Applications & Materials
Fiber Laser: Ideal for marking metals, including stainless steel, aluminum, brass, copper, etc. It can also mark some plastics and ceramics.
CO2 Laser: Suitable for marking non-metal materials, such as wood, glass, rubber, acrylic, leather, and various plastics. These lasers have the ability to cut these materials as well.
Diode Laser Primarily used for plastics, some metals, and semiconductor materials. Mostly for light surface marking applications.
In Summary…
The choice between fiber, CO2, and diode lasers for part marking depends on the specific application, desired mark, and material requirements. Fiber lasers excel at marking metals and producing specialty marks (such as annealing, foaming, color change or deep engraving), and they have the speed to support production environments. CO2 lasers are suitable for non-metallic materials and provide a larger working envelope. Diode lasers are cost-effective solutions for basic marking in plastics and certain metallics.